Petone Engineering
Industry 4.0 Case Study

Specialists in structural steel & seismic strengthening
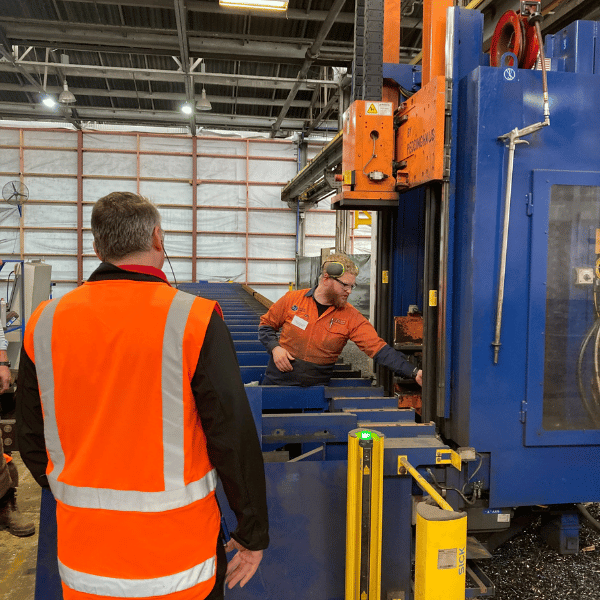
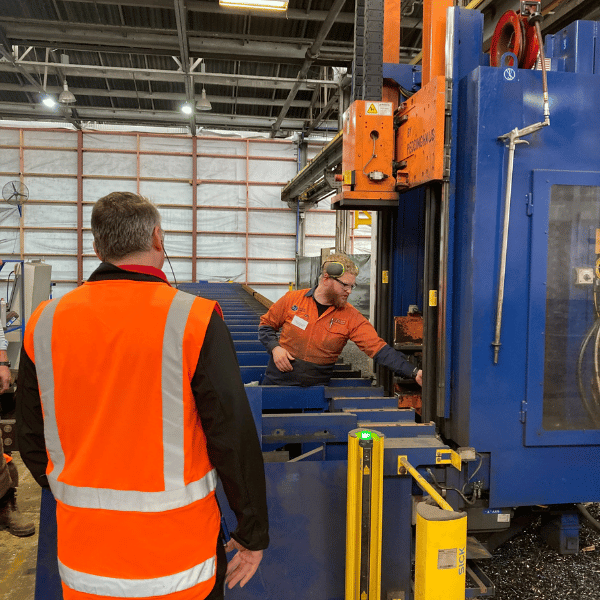
“Empowering teams to undertake the task with simple apps and visuals that avoid language barriers that might exist is essential.”
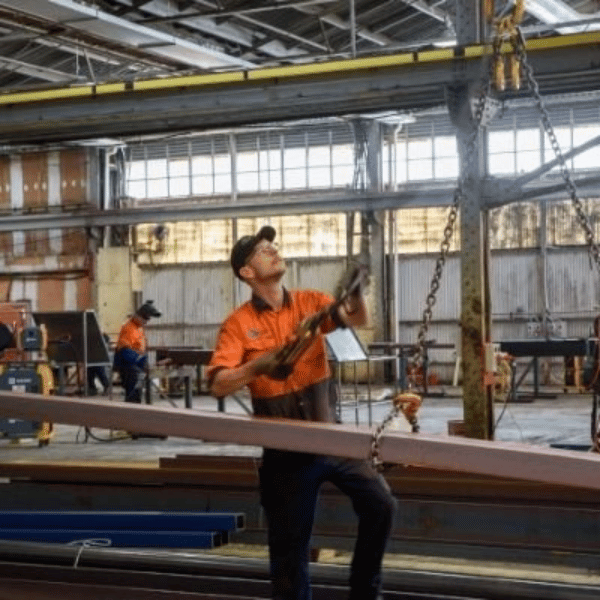
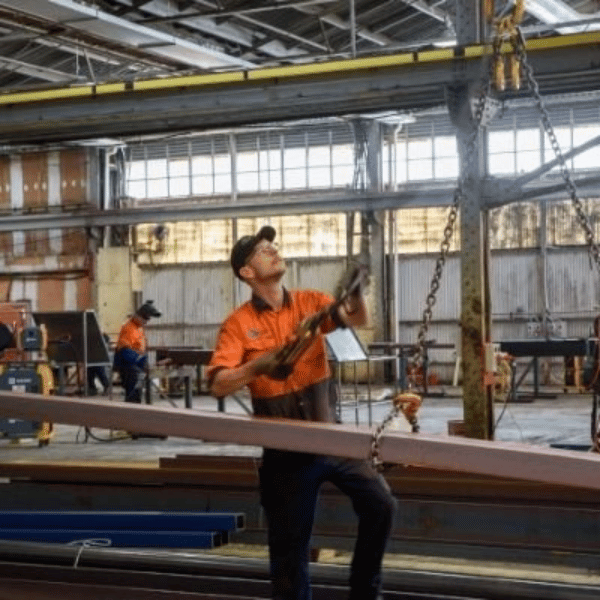
Key learnings
- Exploring the capabilities of existing systems is a must when looking at technology solutions.
- Empowering teams to undertake the task with simple apps and visuals that avoid language barriers that might exist is essential.
- In change management, it is more valuable to educate teams on the ‘why’ of the project than simply the transactional element of delivery. If our teams appreciate the potential impact of using the tool incorrectly, especially in terms of impact it could have on their own workflow down the line.
Background
Petone Engineering have grown rapidly to become a team 60 strong, specialising in medium to large commercial structural steel site erection and seismic strengthening. With capabilities throughout the lifecycle including estimating, detailing, fabrication, welding, protective coatings and site erection Petone have acquired Steel Fabricator certification (SFC) verification recognising their robust processes and quality control.
The company has three core values:
- Being great to deal with
- It has to be right
- All things positive & professional
Petone Engineering’s 3,000 square metre fabrication workshop and office in Seaview, Lower Hutt gives space to run multiple, large scale projects simultaneously, and deliver exceptional quality, cost-effective steelwork to clients on time, every time.
In complex structural steel programmes hundreds of beams and fabrications need to be assembled in the correct order as required by site, often with almost all beams being different. This presents a clear challenge to the production & project management teams – tracking which elements of the build are at what stage.
Breaking the overall building into phases and lots gives structure to communications as to which elements of the build are required in what order. However even within these lots there can be hundreds of components to track.
With the vast majority of components requiring plate and beams to be cut, fabricated, welded and quality checked in between each, whilst all looking similar but being sightly different means a technical solution to track these is beneficial. Especially considering the traceability requirements that all fabrications need to be identifiable as to the team that fabricated, welded and inspected it.
This traceability process was previously managed on paper with signatures and initials identifying who completed various tasks on the drawing that followed the beam around. This was then handled multiple times to transition the data in the right format in the MRP system with the production manager wasting 20 hours per week for an approximately $5000 total spend. Also representing an opportunity for error and single point of failure in the process.
Opportunity
Have as close to real time as possible tracking of completion of each beam and fabrication associated against the master planning information held within the MRP software Strumis. In practical terms, allowing for anyone in the business to get visibility of what stage any particular beam or lot as a whole was up to and therefore what work should be scheduled next on site and across projects.
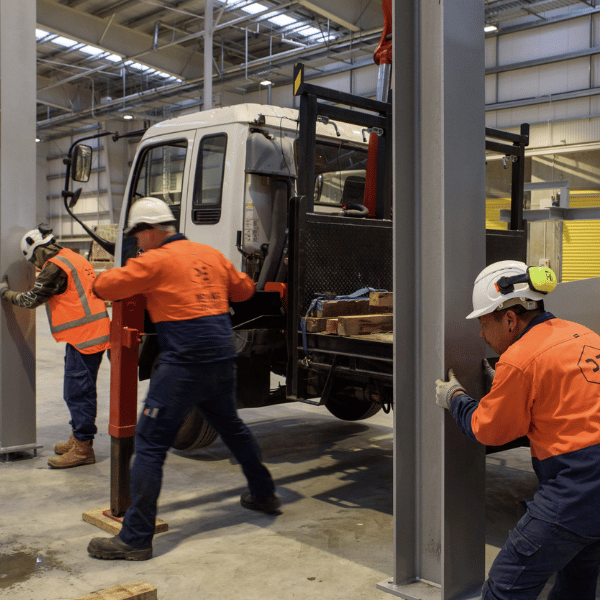
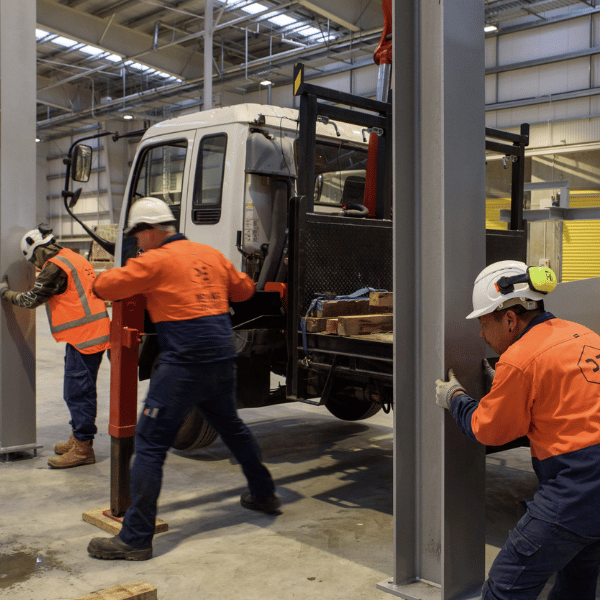
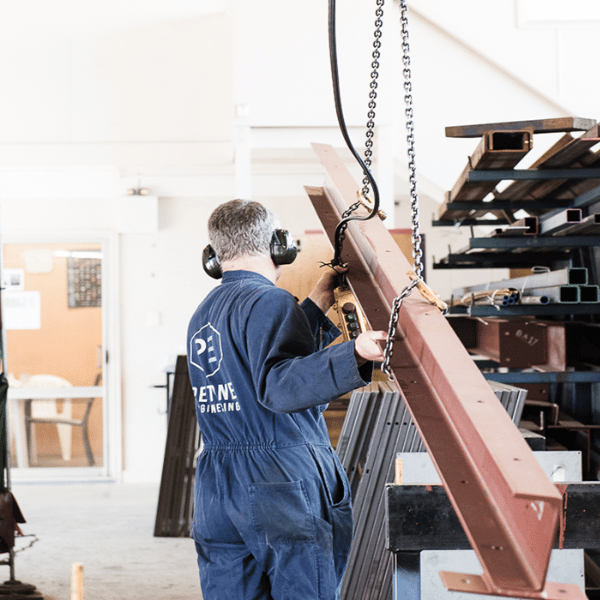
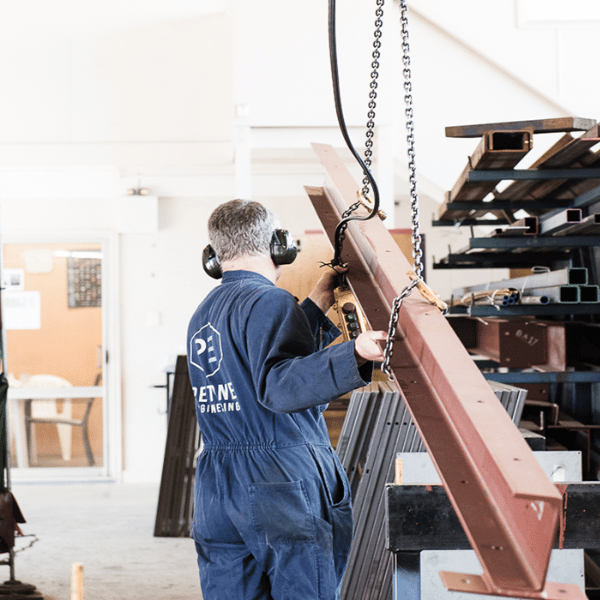
Solution
The team first investigated how to make each beam uniquely identifiable, which presented more challenges than first considered. The heavy engineering environment, cleaning, welding, cutting and painting all mean that marks on the beams themselves would regularly get removed or destroyed. After some investigation, a robust plastic coated label was trialed, containing key information about the beam. This can be cable tied to each beam, whilst staying attached through the process without getting damaged or destroyed.
The key information makes each beam identifiable to the site, subcontract and workshop teams, but also contains a unique QR code identifying the exact beam within the project.
The second stage was linking this barcode through to a basic phone app. This allows scanning at the workcentre to move each job through the process, with the data feedback directly into the MRP system updating the status continuously.
Project Roll-out
The project was done in Kaizen approach, with 2 days of contractor and internal time allocated to implement the project. Hardware was purchased ahead of Kaizen so results could be seen and tested straight away. This was undertaken in this way as the Return on Investment for the project was clear, but for a busy, growing team with varied accountability it wasn’t feasible to free up the time required to learn the technology and then deploy it. Using their network they identified a contractor who had undertaken similar work in the past and partnered the production manager internally to train and learn during the 2 day deployment.
As a technology prerequisite WiFi was going to be needed to support the new process so the relevant infrastructure was put in place to allow for rapid access to the relevant systems on the shopfloor. Results and next shopfloor.
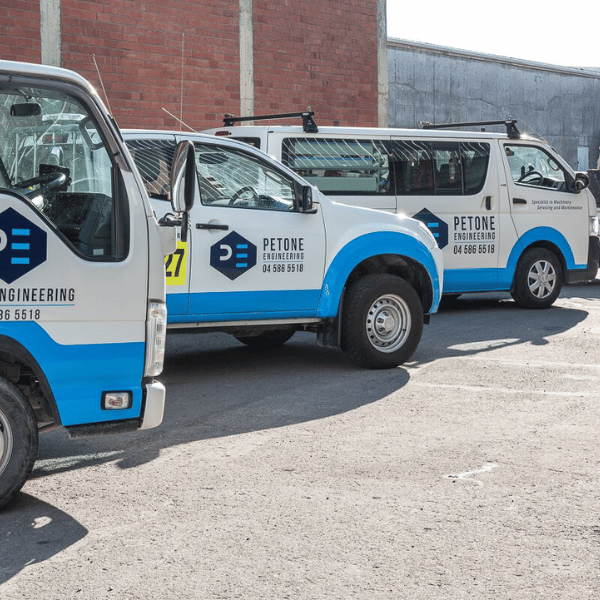
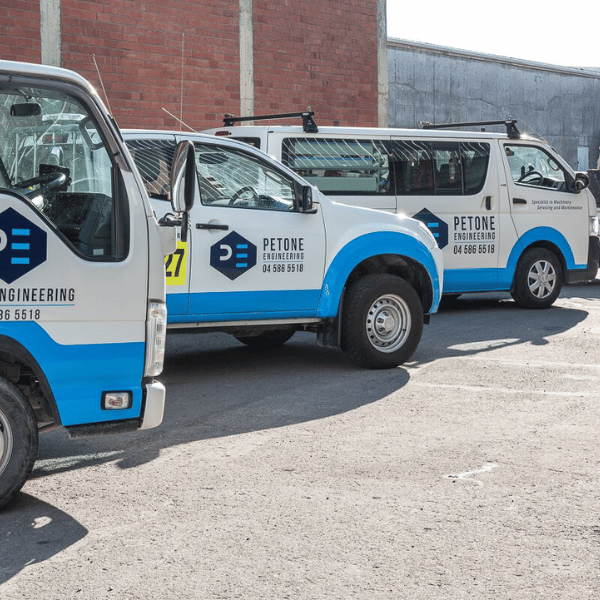
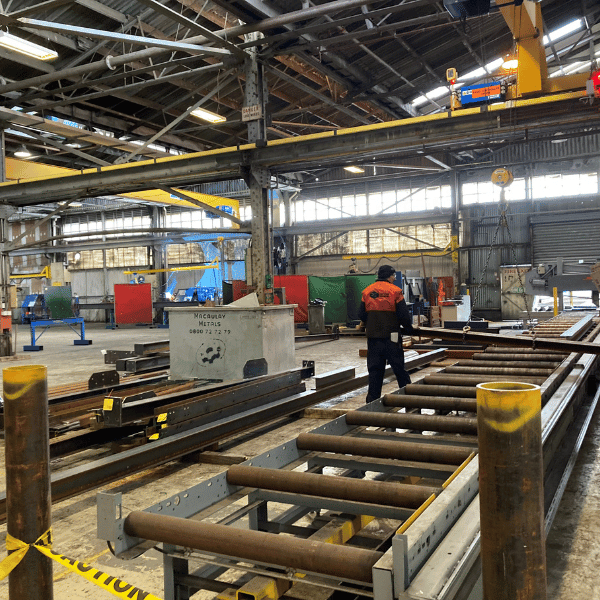
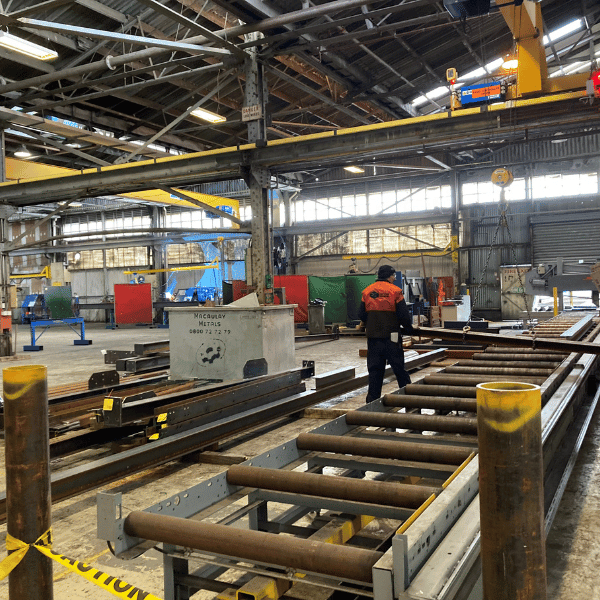
Benefits
The key result has been an increase in the real time nature of the MRP data that drives the business, whilst reducing the admin time for the production manager by around 20 hours a week, who now has more free time to spend on higher value tasks such as planning capacity requirements and training.
Next steps are to roll out the solution to delivery dockets, site delivery and painting Quality Assurance, and finally site erection so that every single stage of the process for a beam is recorded close to real time.
About the site visits and Industry 4.0
The purpose of the Demonstration Network is to drive uptake of Industry 4.0 technologies among New Zealand manufacturers with the aim of increasing their productivity and global competitiveness. The Network of Sit Visits (NSV) are part of the Industry 4.0 Demonstration Network, which also includes a mobile showcase and smart factory showing cutting-edge Industry 4.0 technologies in action. The NSV takes selected companies through a fully funded assessment process to help them accelerate their own journey towards Industry 4.0, and sees them share their knowledge with other manufacturers.