ES Plastics
Industry 4.0 Case Study

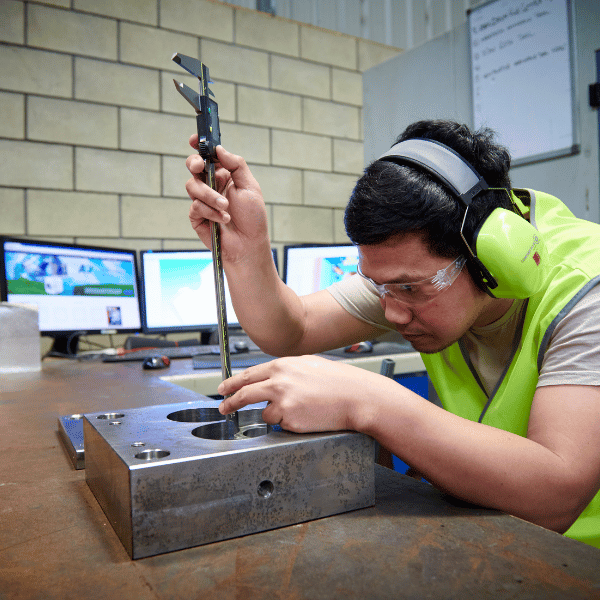
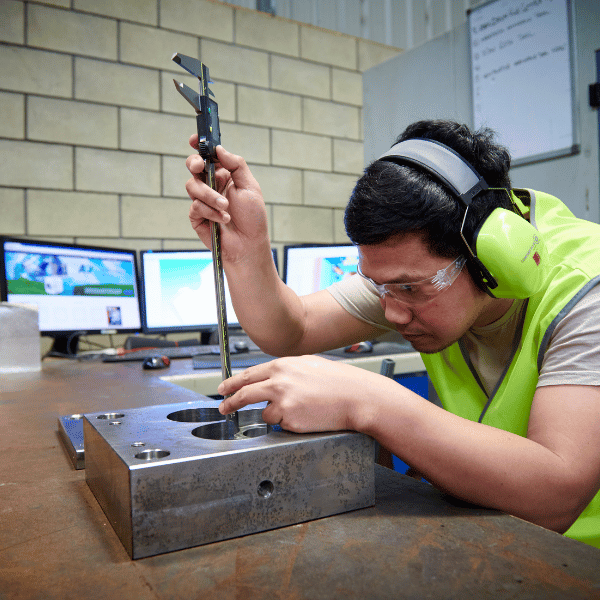
“By having data available to the whole team, it reduces frustrations in accessing information and dependencies on team members.”
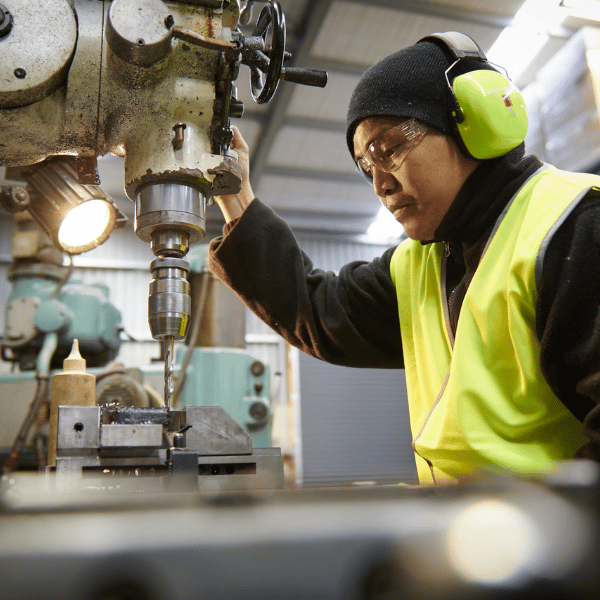
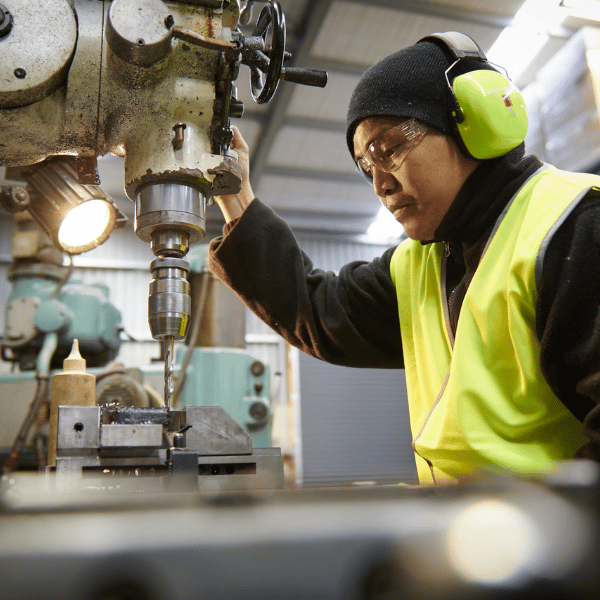
Key learnings
- Improved efficiencies – the business can pivot more quickly to resolve issues. • Reduced complaints – by logging issues, revisions can be made between runs minimising the risk of repeat errors.
- Improved profitability – by reacting quickly to performance or quality issues the team can easily minimise their impact.
- Big data capture – even if they don’t use all the data on the day it’s generated, it allows them to analyse trends in historic performance and implement improvement projects.
- A better place to work – by having data available to the whole team it reduces frustrations in accessing information and dependencies on team members.
Background
ES Plastics is an independent family-owned New Zealand plastics company located in Hamilton. Known for the development of products across a broad range that require strong design, ingenuity and manufacturing ability, ES Plastics has developed a significant customer base, many of whom have been associated with it since its original setup.
Opportunity
Plastic injection moulding and blow moulding operations are typically medium to fast-paced manufacturing environments with multiple machines, which require specific tooling to make each individual product. The tool changes can take days and require skilled resources to fit and maintain them correctly. Planning the runs and raw materials required while keeping track of the tools and the engineering needed to keep them going is a complex task, generating huge amounts of important data in a short time. Twenty years ago the Managing Director Jeff Sharp identified the utilisation of this data was key to his organisation’s success. The key objective of the software was to develop a centralised source of all the information within the business. This would allow the team to make faster data-driven decisions to successfully manage the dynamic business.
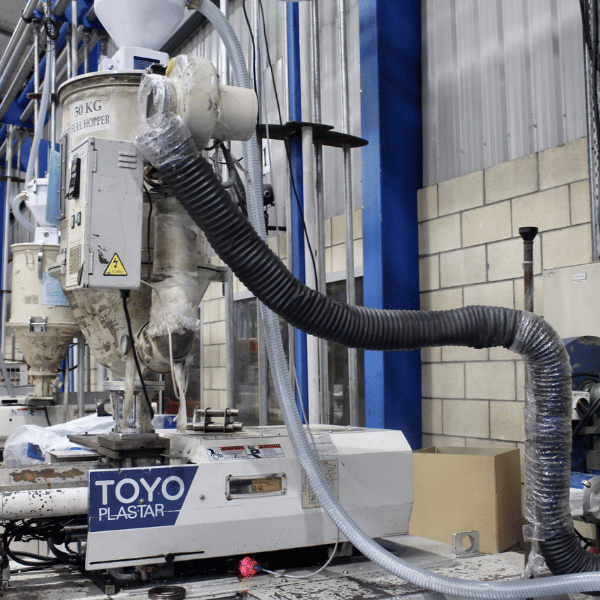
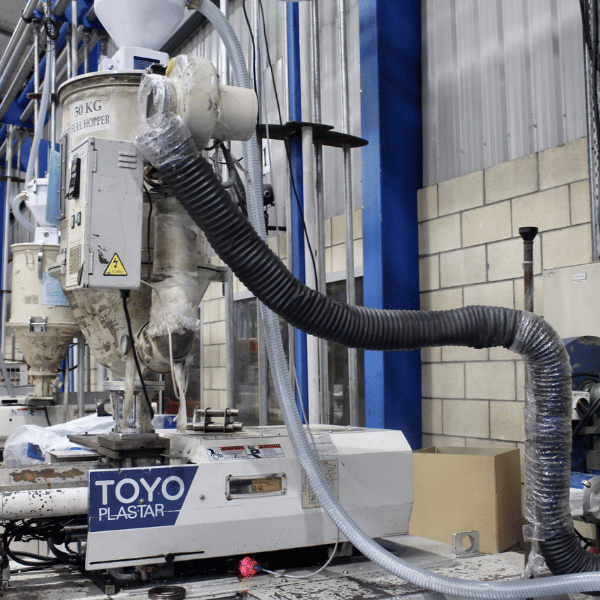
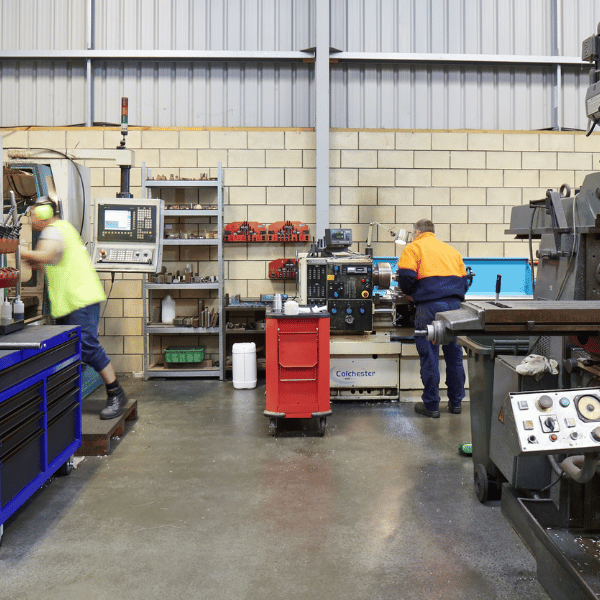
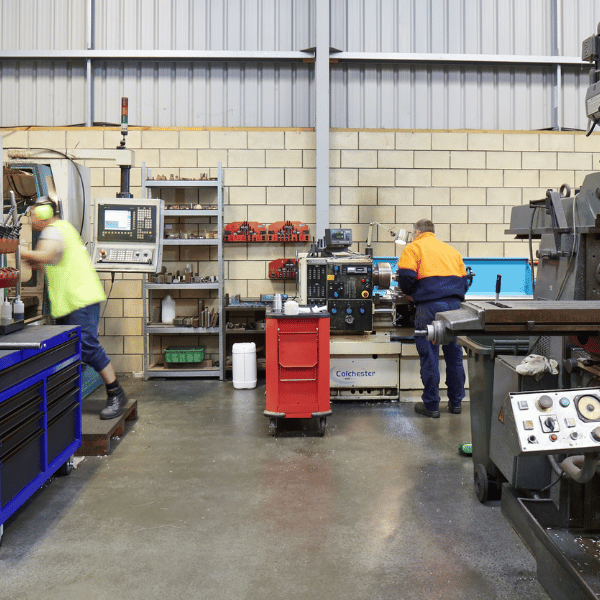
Solution
The solution was to create an in-house data collection system and database with interfaces for operational tasks. This system is called a MES. A MES (Manufacturing Execution System) is a computerised system that tracks and gathers real-time data about the production process on the factory floor. It monitors the machines and data flows involved in transforming raw materials to finished goods. The main goal of a MES system is to optimise and improve production output and
efficiency.
Step 1: Data collection
The first hurdle was data capture. This important data was being generated across multiple machines on the production floor for every cycle lasting roughly between five seconds and five minutes.
Using in-house capability, the team and their business partners were able to develop a solution to connect their machines to a centralised server, allowing the real time machine data to be captured and stored for analysis.
Step 2: Data analysis
While captured data is useful, the real benefit of the investment is unleashing the power of these numbers into a format that allows easy interpretation of the data when it had deviated from defined parameters. Within the SIRI framework this is represented by the shopfloor intelligence dimension.
The team at ES Plastics have developed a dashboard showing the performance of the job on each machine using a traffic light system illustrating performance by time. The system also looks at the standard times for tool changes and highlights deviations.
One of the more advanced features is the labour planning aspect where the attributed labour per job is used to calculate the number of machine operators required for each shift, enabling the operations team a dynamic staffing model which can allow them to optimise their labour efficiency shift by shift.
Step 3: Integration
One of the key benefits of the MES is that all the data from a run is available to the whole business in one place. This is a principle known as vertical integration.
Operator clock in and out is integrated with a third-party software and allows the team leaders to see who is on site, who is on overtime and who hasn’t clocked in for a shift. With the data visible the team leaders can act quickly to identify and correct problems or bring in extra staff to cover shortages.
Quality notes and continuous improvement ideas are also captured and logged onto the job. Whenever a new order for the product is raised the notes are flagged, giving the engineering team time to resolve issues, maintain tooling or support the start-up of the job in the case of quality or re-work errors.
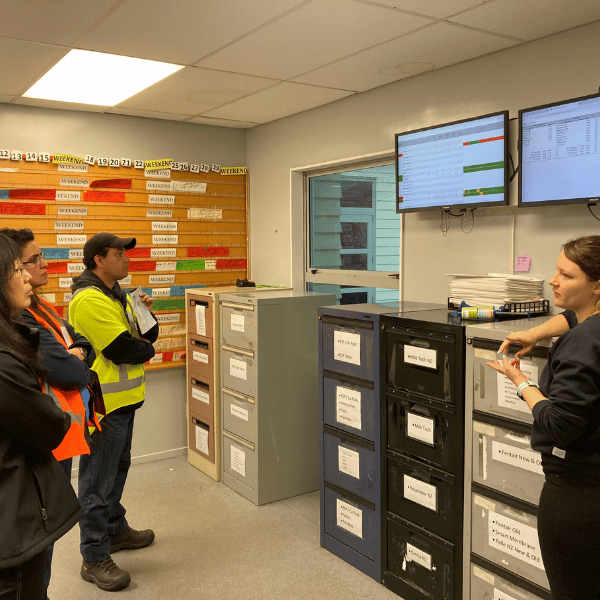
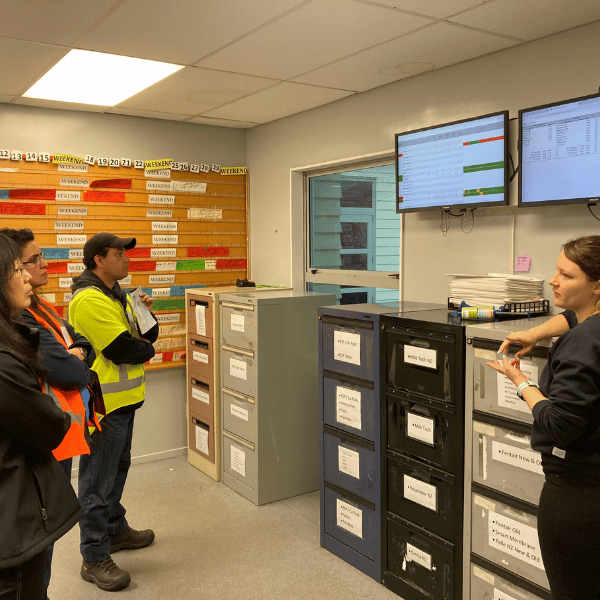
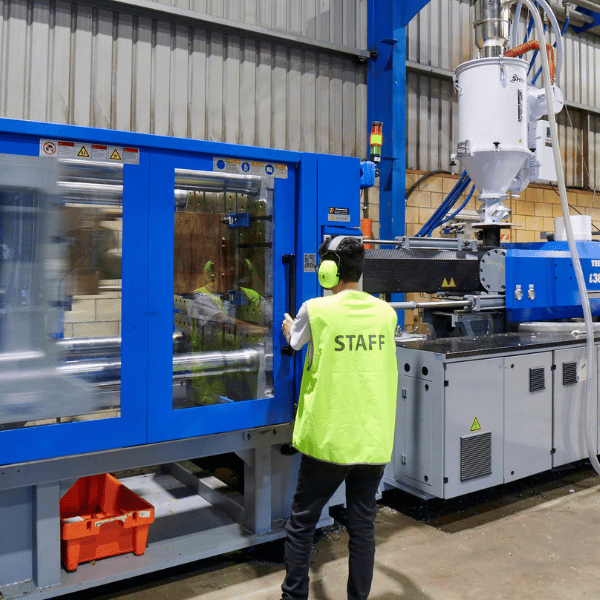
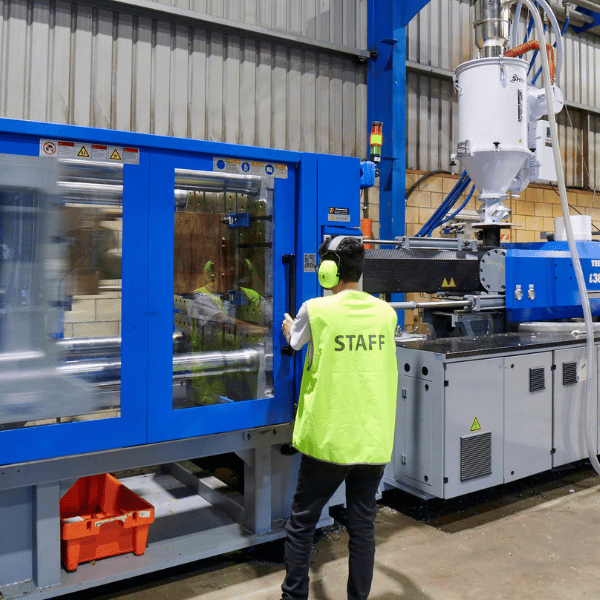
Benefits
About the site visits and Industry 4.0
The purpose of the Demonstration Network is to drive uptake of Industry 4.0 technologies among New Zealand manufacturers with the aim of increasing their productivity and global competitiveness. The Network of Sit Visits (NSV) are part of the Industry 4.0 Demonstration Network, which also includes a mobile showcase and smart factory showing cutting-edge Industry 4.0 technologies in action. The NSV takes selected companies through a fully funded assessment process to help them accelerate their own journey towards Industry 4.0, and sees them share their knowledge with other manufacturers.