Argus ManuTech
Industry 4.0 Case Study

Enhancing Manufacturing Quality and Productivity with a ‘Foil’ Proof Solution!
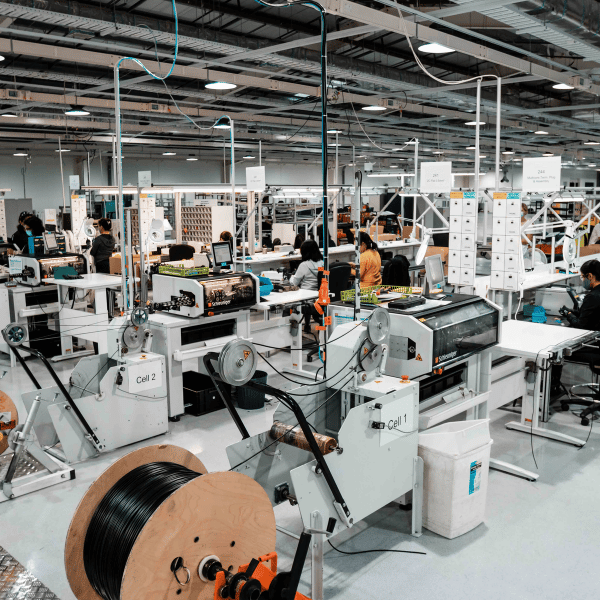
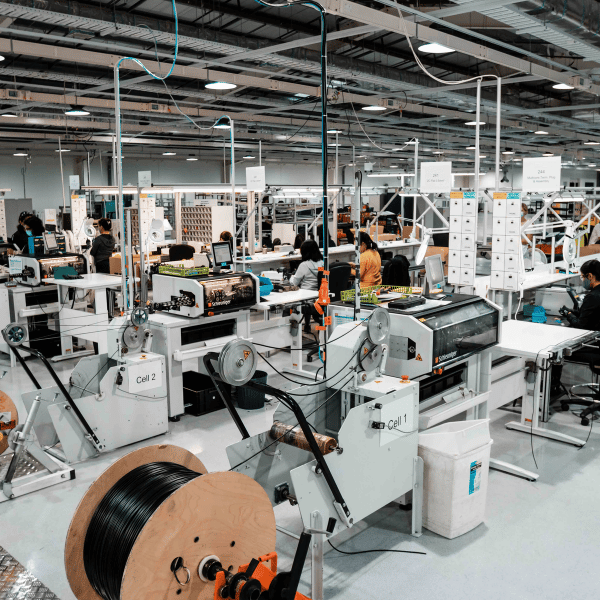
“A cross-fucntional team came together to develop a robust connected quality test system that incorporated industry 4.0 principles to enhance product quality.”
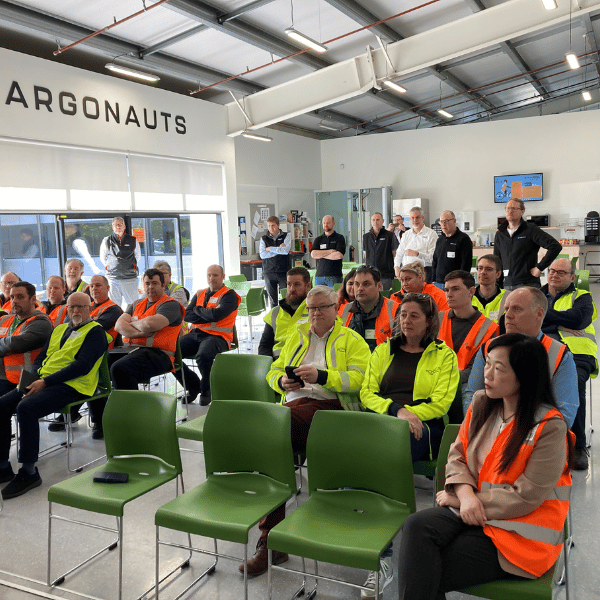
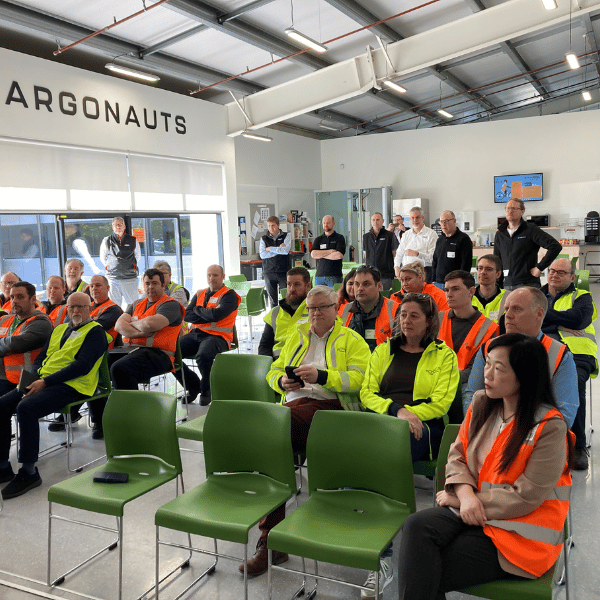
Key learnings
Being involved with an in-house design/build project is incredibly rewarding for team members’ skills development and implementing a positive culture. Approaching the project with a strategic consideration of the test systems life-cycle is important as long-term implications including scalability and adaptability can help ensure lasting success and keep development costs to a minimum.
- Develop the ability to view First Pass Yield (FPY) & overall Yield data in real-time and display them visually on the factory floor.
- Investigate the use of technology to identify which assembly line the product was manufactured on.
- Transition results to a SQL database to support larger data volumes and improve analysis query load times.
Background
Argus ManuTech is an innovative manufacturing company in Christchurch, New Zealand, supporting various Argus Group companies with R&D, manufacturing, and logistics. Their modular manufacturing operation adapts to diverse industry requirements, producing high-quality products using advanced lean principles. With a focus on innovation, Argus ManuTech’s R&D engineers lead the way in driving industry innovation and designing custom products for clients. Their agile production facility and manufacturing engineering support enables an efficient response to customer demands. Argus ManuTech prioritises quality, exceeding industry standards and ensuring compliance with regulations. Their dedicated logistics team ensures seamless supply chain management and reliable product delivery. As an integral part of the Argus Group, Argus ManuTech delivers top- notch manufacturing solutions and technical support to meet diverse client needs, setting new standards in the industry.
Opportunity
Recognising the importance of product quality, the team at Argus ManuTech identified an opportunity to improve the availability of test information for one of their key products. They believed that by doing so, they could achieve significant quality improvements. The introduction of a new IBC foil heater gave them the opportunity to design and implement a connected quality test system. This product required manufacturing to a new world-class specification, rendering the original quality test procedures and equipment inadequate. The team also saw this as a chance to enhance productivity and ergonomics in the manufacturing area dedicated to these products. A prototype test solution was designed and implemented but it was unsuitable for full production due to several issues, including non-intuitive operation for production staff, a lack of adaptability to process changes, and insufficient guarding. Additionally, the associated electrical safety tester did not possess the required data capturing capability that was mandated by the new requirements and desired by the team for process improvement and product quality feedback.
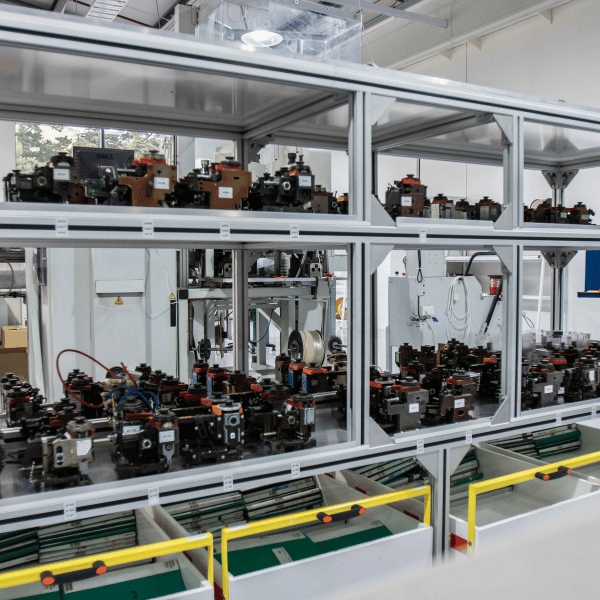
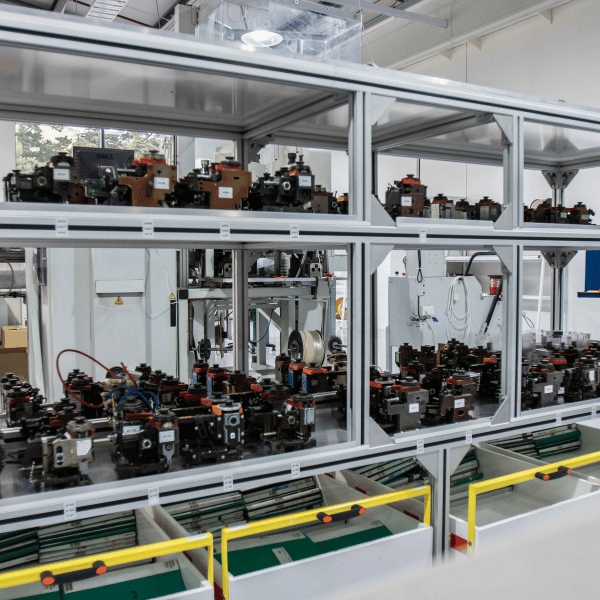
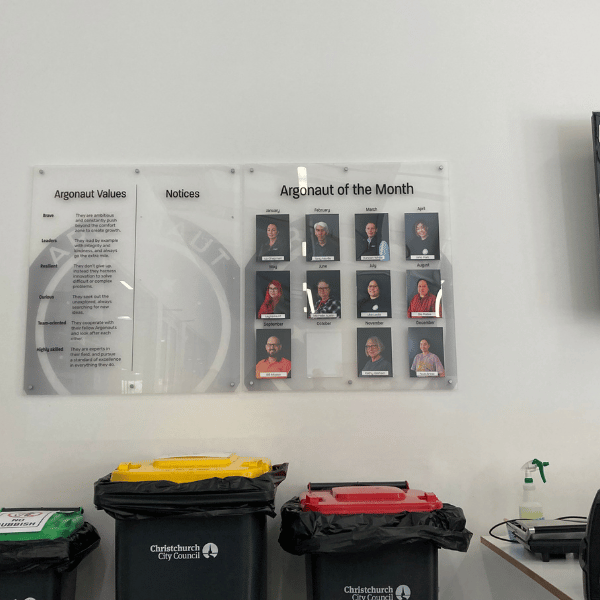
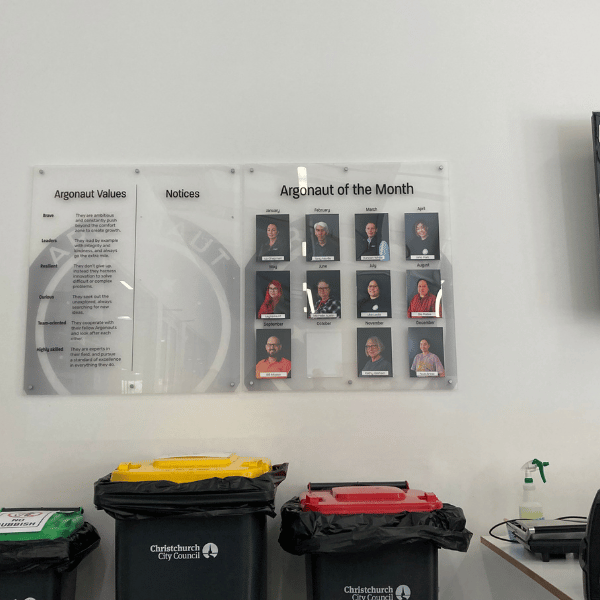
Solution
A cross-functional team came together to develop a robust connected quality test system that incorporated Industry 4.0 principles to enhance product quality as well as redesigning the line to improve productivity and ergonomics. The solution incorporated a custom software interface, durable industrial build quality, improved safety features, an adaptable design, and the capacity to enable advanced data analytics. The key features of this solution were as follows:
- Custom Software: Hardware is controlled via a user-friendly interface developed in National Instruments LabView that also captures data from the Electrical Safety Tester and stores it as a CSV file. This simplified testing by automatically initiating tests when the interlocked guard closed, displaying system status and pass/fail results. Industrial
- Build Quality: The project emphasised industrial-grade construction, utilising components from trusted manufacturers such as Festo, Schneider, Siemens, and Omron. The hardware exhibited durability, while the software was built using National Instruments LabView.
- Robust Pneumatic Guard: The team designed a custom guard to enhance station durability and ensure safety during testing.
- Safety Measures: Safety was a primary focus, incorporating two-handed control, a monitored emergency stop circuit, non-contact safety switches for the interlocked cover, and an ANDON tower for status indication. In addition, the team ensured the incorporation of the following considerations:
- Adaptable Design: The test station was designed to accommodate future product and process changes. It utilised modular aluminium extrusion and the control system employed a programmable logic controller (PLC) for potential product portfolio expansions.
- Maintenance: Hardware choices were made to minimise component failure, with on-site replacements available. The control cabinet utilised standard wiring techniques for easy troubleshooting, and the electrical system was fully documented.
- Operator Interface: The interface was designed to be intuitive, featuring two-handed control, continuous safety monitoring with an Omron Safety Relay, and a PC monitor for status/results.
- Modular Assembly: Construction employed modular aluminium extrusion, simplifying modification without custom brackets. The guard consisted of a steel square section with polycarbonate guarding, offering rigidity and impact resistance.
- Hardware Expansion: The hardware facilitated future test capability expansion, featuring spare inputs/outputs in the PLC for control upgrades.
- Data Analytics: Test data is automatically exported as CSV files for each test cycle and processed in PowerBi for analysis.
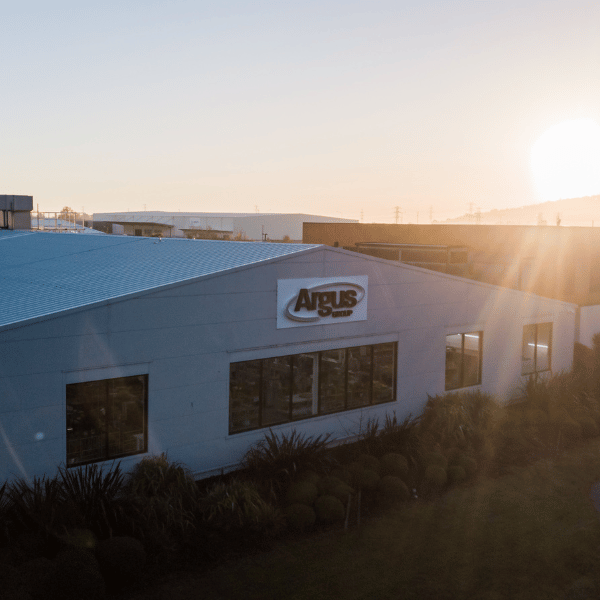
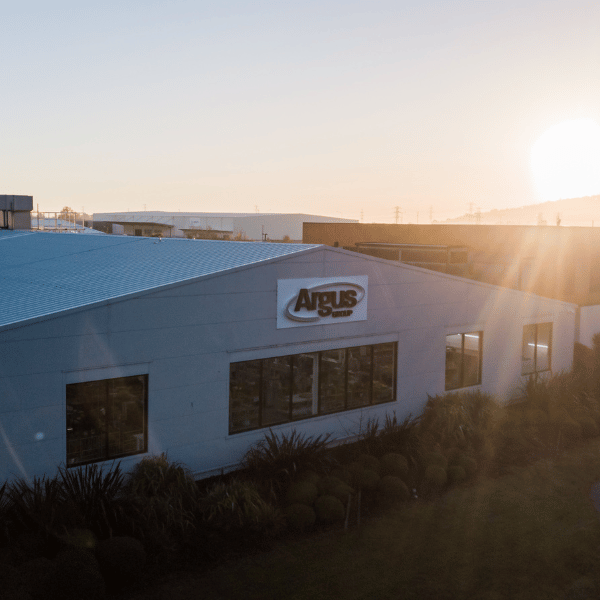
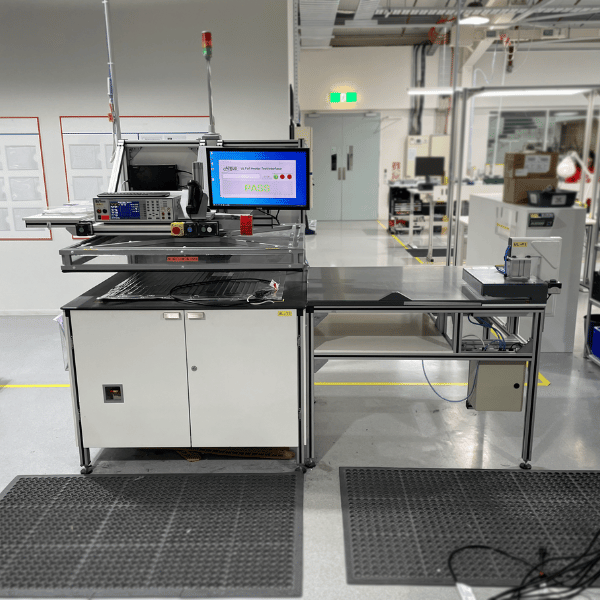
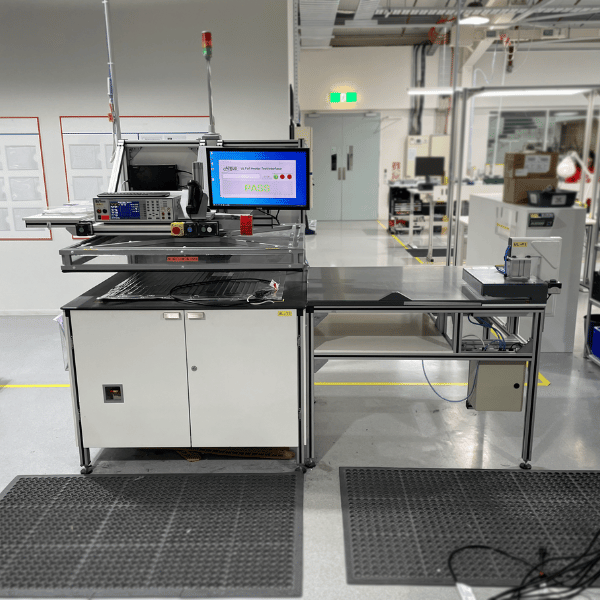
Benefits
- Analysing defect data has led to an increased understanding of upstream manufacturing processes as targeted root cause investigation work could be performed.
- This approach led to foil heater defect PPM & CoPQ reducing by 47% and First Pass Yield increasing from 94% to 97% since November 2022.
- Successfully implementing this test system has increased our team members’ knowledge, skills, confidence, collaboration, and pride in their work.
- Additional improvement opportunities have been identified that would not have been considered previously due to being deemed cost-prohibitive if performed by an external company.
About the site visits and Industry 4.0
The purpose of the Demonstration Network is to drive uptake of Industry 4.0 technologies among New Zealand manufacturers with the aim of increasing their productivity and global competitiveness. The Network of Sit Visits (NSV) are part of the Industry 4.0 Demonstration Network, which also includes a mobile showcase and smart factory showing cutting-edge Industry 4.0 technologies in action. The NSV takes selected companies through a fully funded assessment process to help them accelerate their own journey towards Industry 4.0, and sees them share their knowledge with other manufacturers.